In this article, we will provide a brief overview of some of the history related to relief valves and how we document them. Because this is an introductory article, there are some simplifications of concepts and language. For ease of reading, we are describing many different types of relief valves, including conventional, balanced bellows, and pilot operated, simply as “relief valves” for this article.
An Introduction to Relief Valves
The Importance of Relief Valves
A relief valve is a safety device that protects equipment and piping from failure due to overpressure. Virtually all manufacturing plants and most of our homes have relief valves; for example, every home has a water heater that has a pressure relief valve to protect from high temperatures and pressures if the controls for the heating element fail.
A little bit of history can help us understand the importance of relief valves on these pieces of equipment, typically referred to as “pressure vessels”.
After the advent of rolled iron plates in 1875, manufacturers began to fabricate significantly-sized pressure vessels. Unfortunately, not a lot of thought went into protecting them from overpressure, resulting in vessel explosions—the force of which resulted in many deaths and injuries. Between 1870 and 1910, about 10,000 major explosions occurred in North America (about one boiler explosion every 36 hours). And though the number of explosions dramatically dropped after 1910, they still occur, causing injury, loss of life, and astronomical financial losses. Between 1955 and 1986, the 100 largest losses in the hydrocarbon and chemical industries cost $820 million in 1986 dollars—that translates to over $21 billion today.
The April 9, 1998 explosion at the Herrig Brothers poultry farm provides a sober example of the damage these explosions can cause. According to the US Chemical Safety and Hazard Investigation Board, an 18,000-gallon propane tank caught fire and exploded, killing two volunteer firefighters and injuring seven other people. The propane tank fire started after an all-terrain vehicle crashed into unprotected above-ground propane piping that ran from the propane storage tank to process equipment. The collision triggered a propane leak under the tank, which eventually ignited and engulfed the tank. Because of the fire’s size, firefighters could not approach a manual shut-off valve to stop the leak, so they decided to spray the surrounding buildings to prevent the spread of fire and just let it burn itself out. Unfortunately, the fire engulfing the tank heated up the propane inside, building pressure until it ruptured and propelled fire and debris over 100 feet, killing two firefighters and injuring seven emergency response personnel in the vicinity of the propane tank. Two key problems led to this explosion: (1) there was not sufficient protection of the piping around the tank to prevent it from being damaged, and (2) the tank lines lacked an excess flow check valve that is frequently installed to limit un-controlled flow.
Pressure containing vessels must be protected in some fashion from high pressure (overpressure) per their applicable design codes using prescribed means and methods. While the failure rate of pressure containing vessels has gone down since 1875, failures continue to occur. As such, the need for continued education and vigilance is critical.
The Causes of Overpressure
So, what causes the types of overpressure that resulted in the above tragedies and losses? And how can they be avoided in the future?
Generally, it’s possible to overpressure equipment by:
- providing heat or cooling at the wrong time
- providing additional material to a vessel at the wrong time
- having an unplanned chemical reaction
- the failure of utilities to the equipment
- the failure of the automatic controls
Interestingly, the majority of the failures occur during start up and shut down of processes because of transient changes (e.g., leaving a valve open or closed during start up). These failures can be mitigated by good design methodology, installation of properly sized relief devices, and continued maintenance of proper documentation.
Relief Valve Design and Documentation
The design methodology for relief valves was initially developed by a number of industry associations including:
- Compressed Gas Association, CGA,
- Gas Processors Suppliers Association, GPSA,
- Underwriter’s Laboratory –UL 42,
- American Society of Refrigeration and Heating Engineers, ASHRE 15,
- American Petroleum Institute, API 520, 521, and 2000, and
- American Society of Mechanical Engineers, ASME section I and VIII.
A lot of the initial design methodology was simplistic and heuristic-based, consistent with the understanding and tools available at the time. In 1977, the American Institute of Chemical Engineers (AIChE) recognized the need to develop better methodology for reactions and two-phase relief, and set up a group, the Design Institute for Emergency Relief Systems (DIERS), to study and develop the tools to address the issues of relief valve design. Slightly later, the US government recognized that a common minimum design standard for relief design is required, so they codified it with OSHA 1910. One of the requirements is that the design of relief devices be documented. Many of the designs up to this point were documented with minimal descriptions and calculation explanations. Additionally, these designs were frequently not included in the files nor were they updated as the plant design changed.
To document relief devices, there are four elements to consider including: equipment limitations, relief scenarios, the relief device, and the compilation of this information and supporting documentation into a final report.
System Limitations – What is protected?
Each of the pressure vessels, heat exchangers, operating equipment and piping (summarily called equipment) are designed to contain the system pressure. The MAWP for each item has to be considered to find the minimum (limiting) pressure that should be used as the set pressure for the relief valve. Here is an example of how the minimum set pressure can be understood. For the equipment limitations, a table is prepared showing the pressure and temperature limitations for the equipment and piping protected by the relief device. The maximum set pressure for the relief device will be derived from this table, an example of which is provided below:
Protected Equipment | Design Pressure | Design Temperature | Limiting Condition | |
---|---|---|---|---|
Number | Description | PSIG | F | |
PR-100 | Feed Tank | 100 | 100 | Y |
PR-101 | Feed Tank Heater | 250 | 200 | |
PI-CS150 | Pipe Specification | 276 | 100 |
Relief Scenarios – What causes over-pressure?
Each of the determined causes of overpressure mentioned earlier result in a relief scenario that must be evaluated to determine the minimum relieving rate and the subsequent open area necessary to ensure the MAWP is not exceeded. The relief scenario that produces the largest required relieving area then serves as the basis for the actual relief device and its associated open area. Based on the selected device’s actual open area, the inlet/outlet piping may be sized or evaluated to ensure compliance with maximum allowable pressure losses in each.
Relief Device
There are a number of device types that can prevent the pressure buildup including:
- Conservation valves—valves that open at designated pressures and will reclose at low pressures. These are for low pressure vessels (< 15 psig)
- Rupture discs—a light plate across the pipe that ruptures at designated pressures. The plate has to be replaced to close the vessel off again.
- Relief valves—valves that open at designated pressures and will reclose at low pressure
- Rupture pin devices—valves that open at designated pressures as a pin bends. This device requires replacement of the pin to reclose.
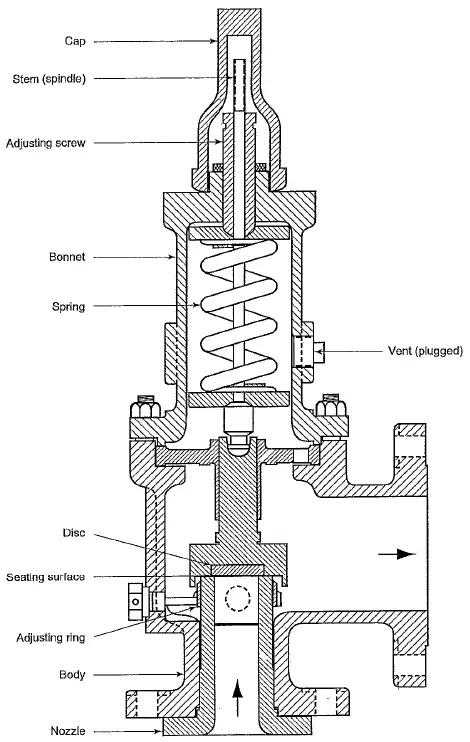
Relief Valve
A relief device document is prepared to show the equipment that is protected by a relief device, the evaluation of the relief scenarios, and the specification of the device. Supporting documents including the piping and instrument drawing (P&ID), the piping isometrics, the physical properties of the relieving stream, and the pressure drop through the inlet and out piping. It is critical that the owner maintains the documentation in their plant files. As changes are made to the plant, the relief device document must be updated to match.
OSHA continues to provide minimum standards for relief documentation, and they also verify compliance with the documentation of relief devices within specific industries following equipment failures.
Want to Learn More?
This article provided a historical look at the development and impact of relief valves, their design, and the necessity of proper documentation for safety, but it was not an exhaustive look at the full range of possibilities of design and safety for pressure vessels. Matrix Technologies is one of the largest independent process design, industrial automation engineering, and manufacturing operations management companies in North America. To learn more about our process design services, contact Jeremy Runk, Department Manager of the Process & Electrical Design Department.
© Matrix Technologies, Inc.